FORGINGS
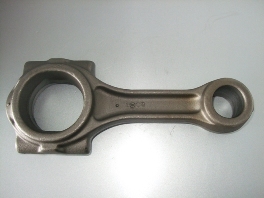
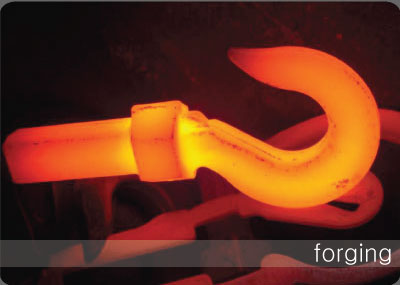
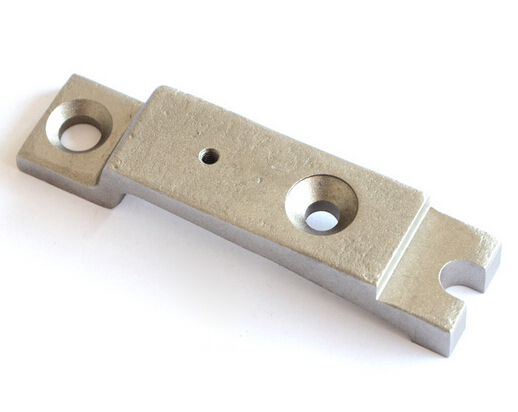
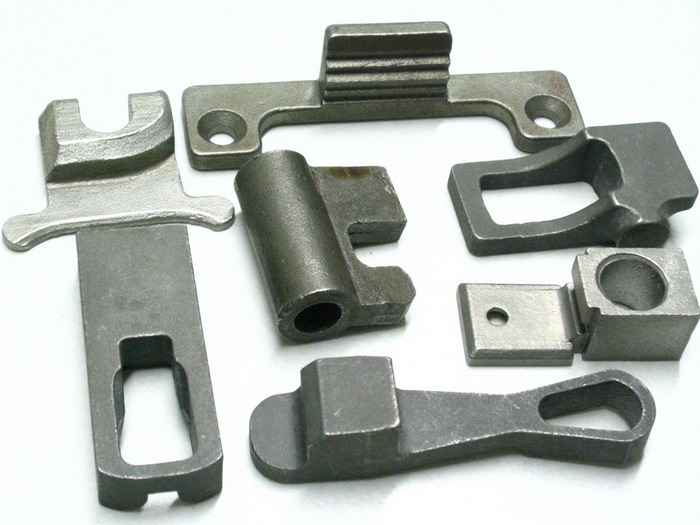
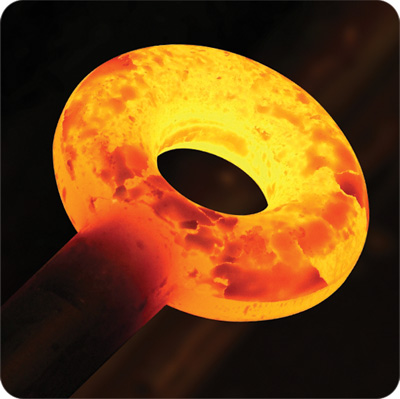
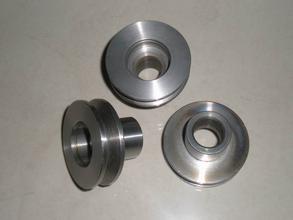
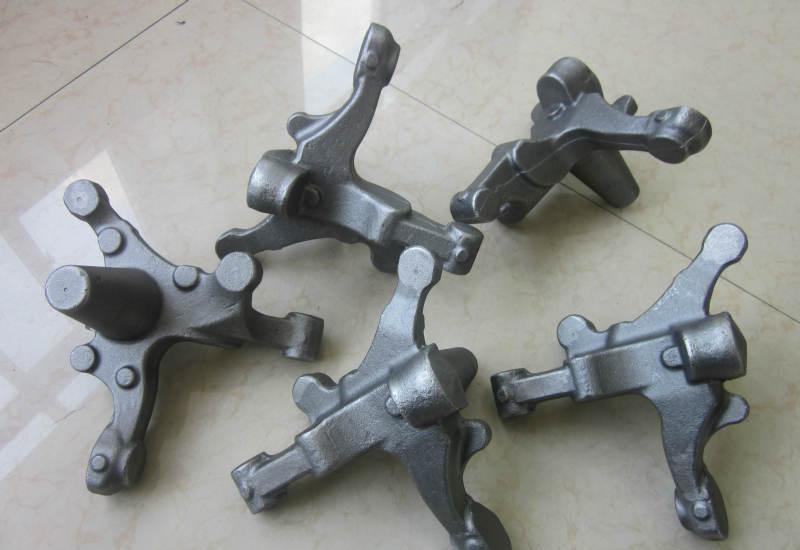
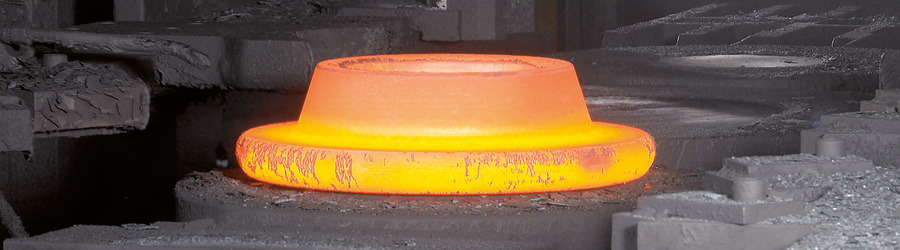
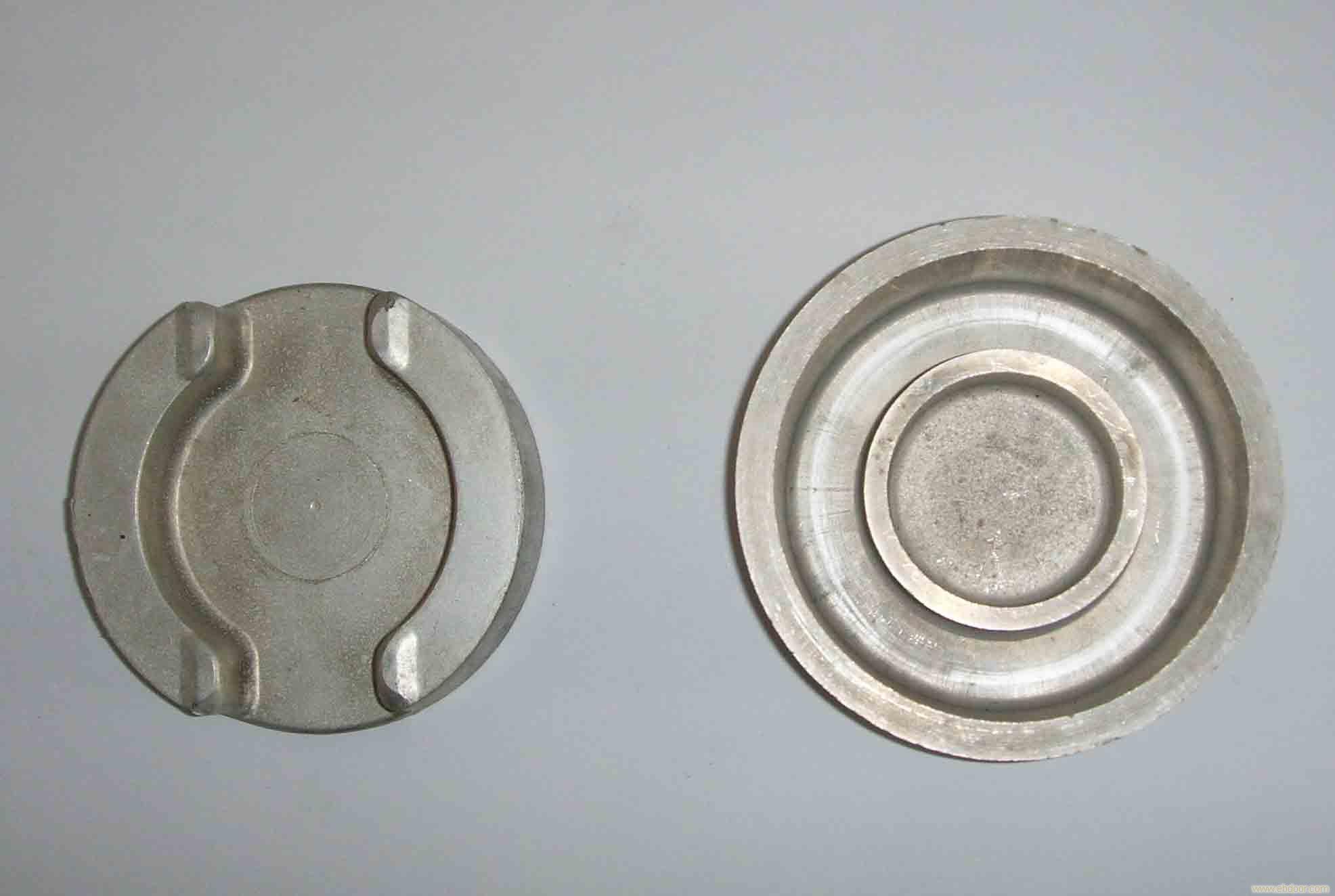
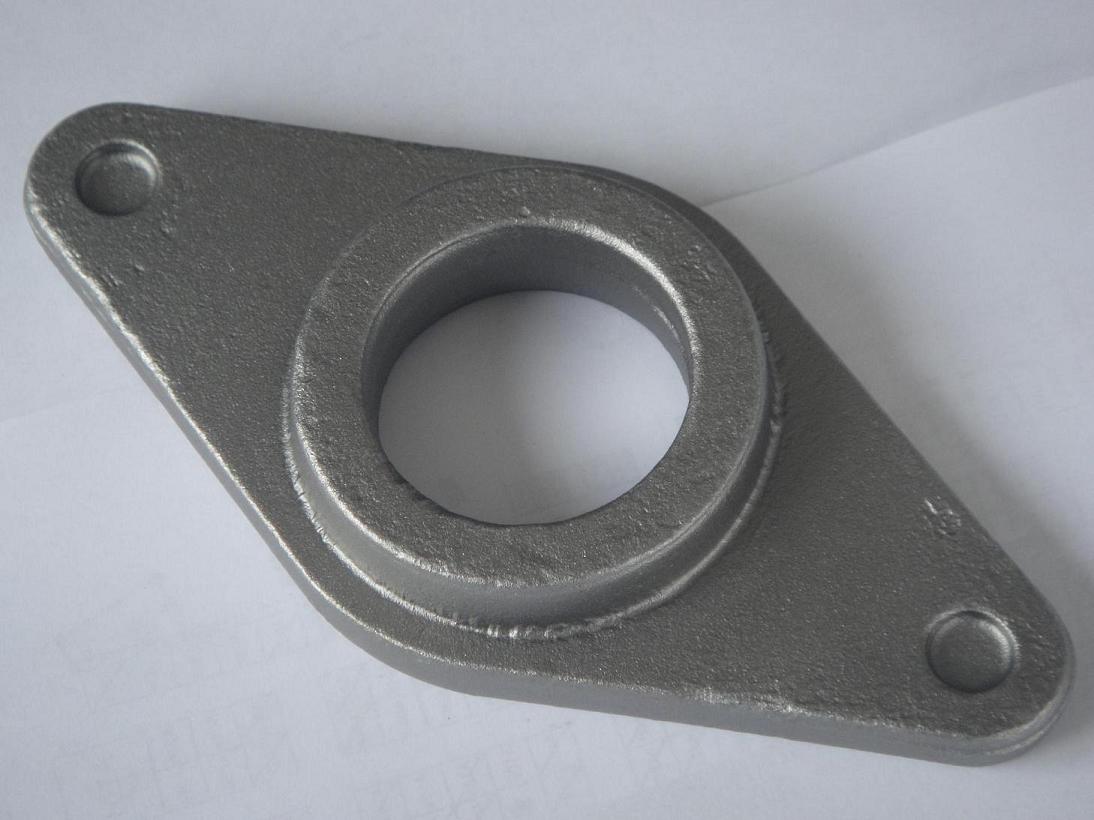
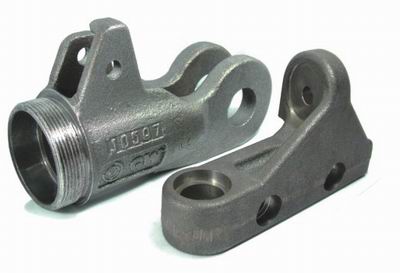
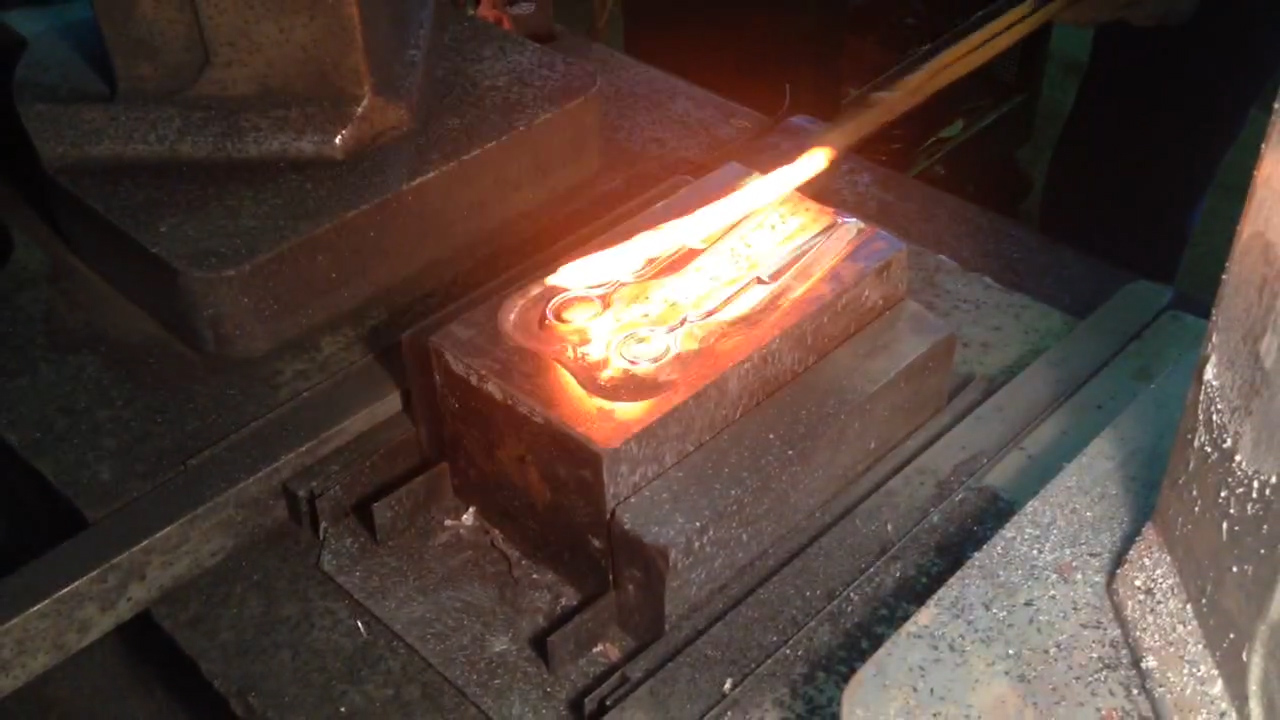
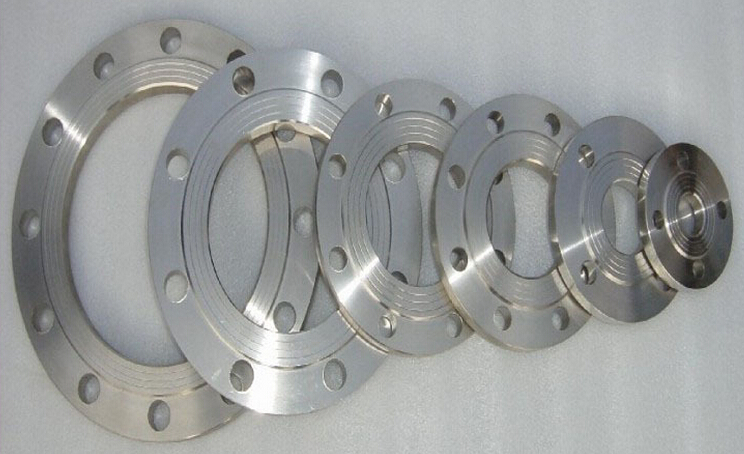
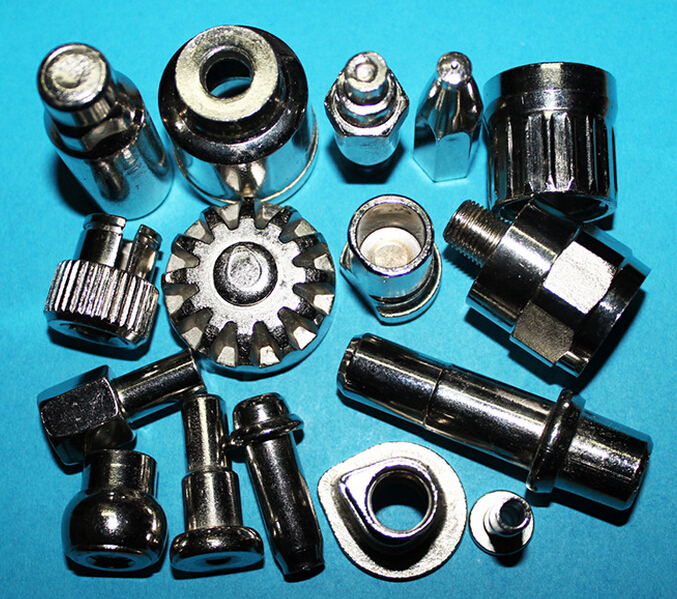
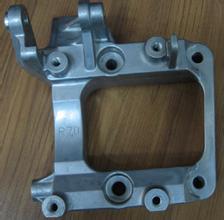
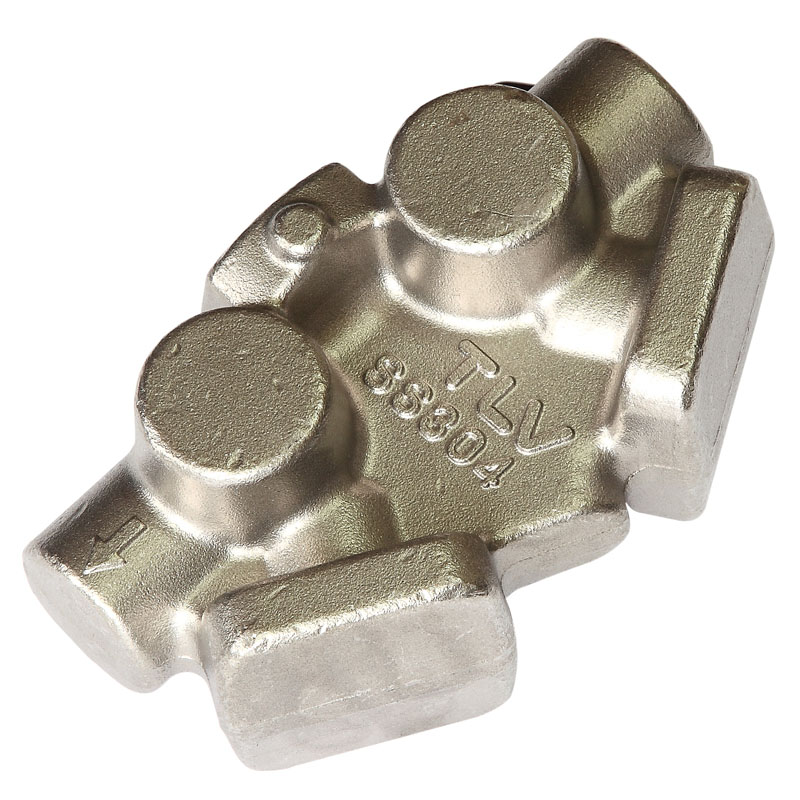
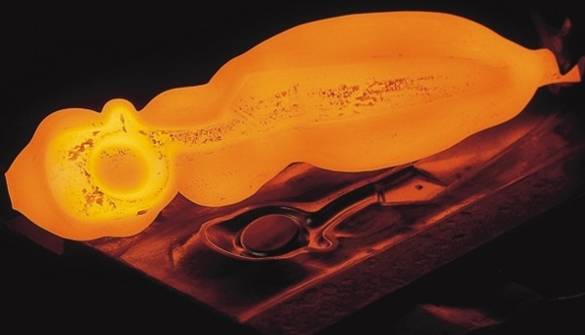
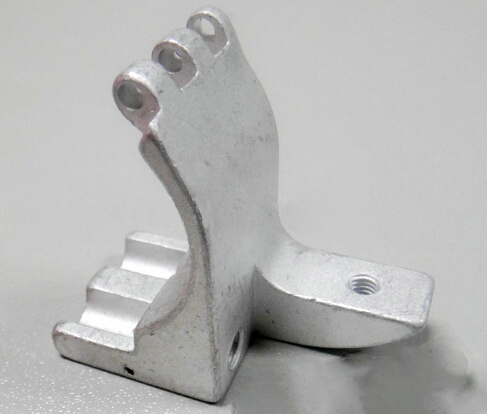
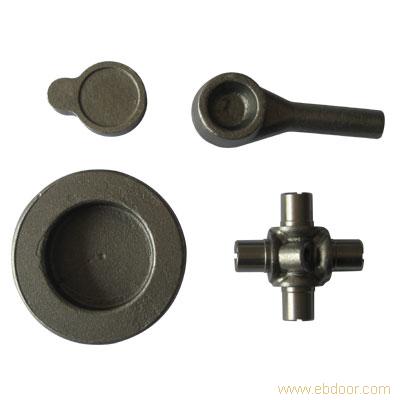
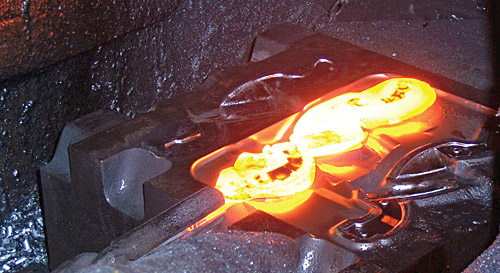
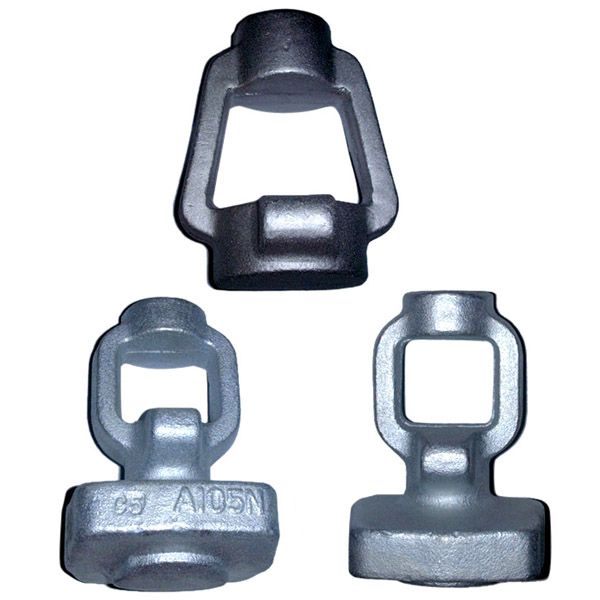
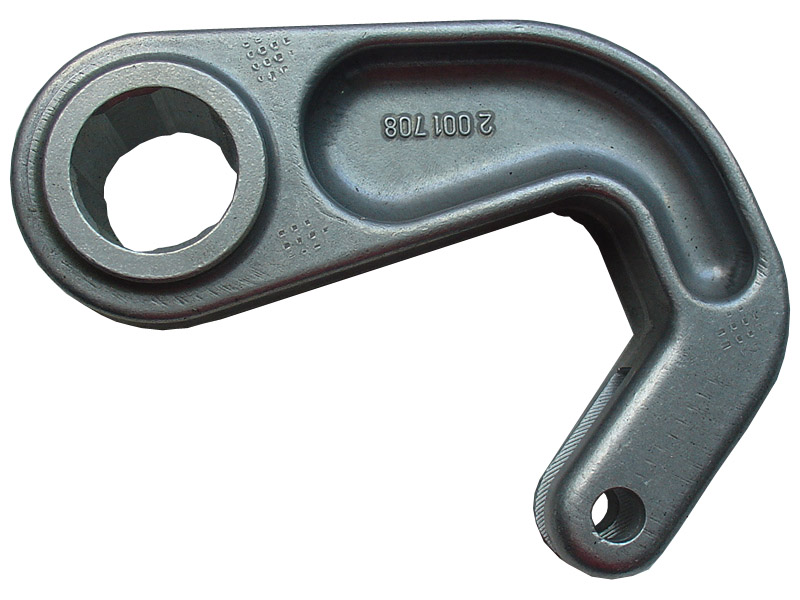
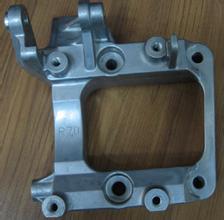
Aluminum Forgings
— Aluminum forgings are the product of a metallurgical process in which aluminum is given a particular shape by the application of a compressing force. The forging process strengthens the metal by changing its grain structure to conform to the shape of the part, and thus yields a stronger final product than welding, casting and fabrication.
Aluminum forgings possess a smooth appearance, good fracture resistance, good thermal and electrical conductivity and are relatively economical .
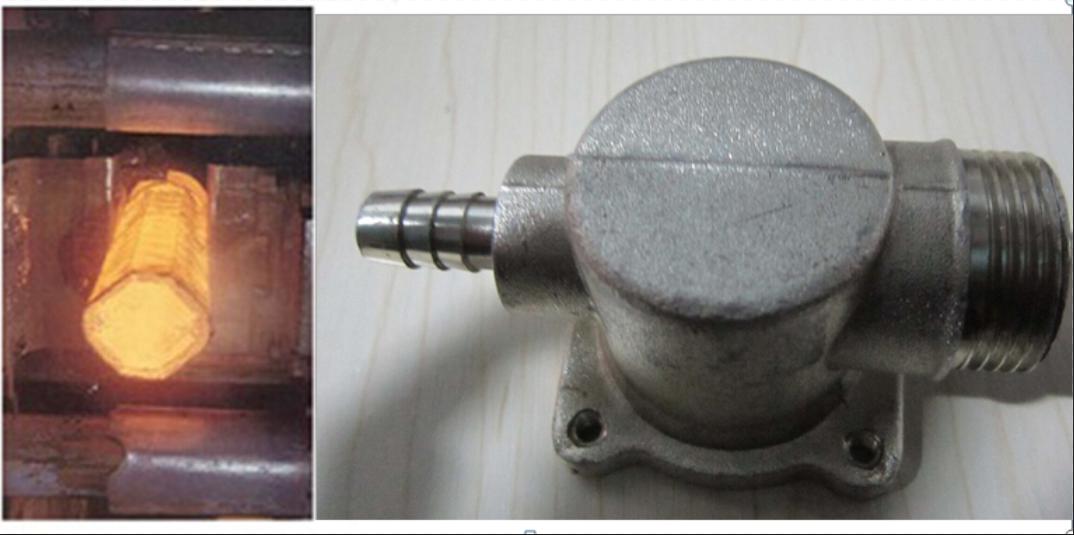
Carbon Steel Forgings — Carbon steel forgings are created through the metallurgical process of forging, in which carbon steel is given a particular shape by the application of a strong compressive force. The metal forging method creates the strongest and most reliable carbon steel products available by deforming the grain of the metal to take on the shape of the part. Carbon steel is a ferrous alloy whose main alloying element is carbon, but it can also contain limited amounts of copper, manganese and silicon. The carbon gives the steel greater hardness and strength, particularly when the steel is heat treated. Carbon steel is quite malleable, and therefore is easily processed and readily forged.
Closed Die Forging — Closed die forging, also known as impression die forging, involves the pressing or hammering of preformed metal blanks into a set of dies shaped as a three dimensional negative of the part to be produced. In closed die forging the hammer and anvil fully enclose the workpiece, forcing the metal to fill all areas of the die. Closed die forging can produce a nearly limitless variety of 3-D shapes, and is capable of producing complex parts with tight tolerances. Closed die forging is distinct from open die forging, in which the die only comes into contact with part of the workpiece at a time.
Cold Forging — Cold forging, also known as cold heading, is a metal forming process that involves the plastic deformation of metal by squeezing the material through an open die using an unheated billet and causing the finished part to assume the shape of the die. Unlike most forging, which is performed hot at temperatures nearing or exceeding 2300 degrees F, cold forging is performed at below the re-crystallization temperature of the metal, at anywhere from room temperature to several hundred degrees F. Cold forging is ideal for the fabrication of many metals .
Copper Forgings — A copper forging is fabricated through a forming process that involves the plastic deformation of copper, a nonferrous material, under pressure and high temperatures through hammering and rolling. Since copper is a ductile metal offering high thermal and electrical conductivity, copper forgings can come in many different configurations including rod, bars, wire, sheets, strips, tubing and more.
Drop Forging — Drop forging is a metal shaping process in which a hammer drops onto an ingot, or metal workpiece, in order to compress it and conform it into the shape of a die or set of dies. Drop forging is the most common metal forging method, and it can be employed in hot forging, warm forging, and cold forging, as well as in both open die forging and closed die forging. This is a modern form of smith forging; the manual force of the blacksmith wielding a hammer has been replaced by a mechanized hardened alloy steel hammer fitted with a specially shaped die. Forging strengthens metal for its particular use by causing the internal grain of the metal to deform to follow the shape of the part.
Metal Forging — Metal forging is a metal forming process that involves the plastic deformation of metal through extreme pressure. Usually metal forging is performed at high temperatures, but it can also be done ‘cold’ at temperatures below the re-crystallization point of the metal. As one the oldest known metalworking processes, metal forging has evolved over the centuries to include innovative and diverse techniques.
Open Die Forging —Also known as smith forging, open die forging uses simply-shaped, non-encompassing dies to hammer or press a metal workpiece into a certain shape. It is distinct from closed-die forging, in which the dies fully enclose the workpiece when they are brought together. The open die forging process allows for larger products to be forged than other types of forging – up to 150 tons and 80 feet long or more. Open die forging is used most often to produce round, square, rectangular, and hexagonal bars, beams and other basic shapes.
Seamless Rolled Rings —Seamless rolled rings are forgings formed from a single “donut”-shaped block of metal by the application of horizontal and vertical pressure. Seamless ring-rolling is a unique type of metal forging that produces seamless metal rings with great tensile strength and structural integrity. Seamless rings may be forged into a wide range of dimensions, from small bearing housings to wind turbine slewing rings.
Stainless Steel Forgings — Stainless steel forging is a method of metal forming by which the metal is heated to a temperature that allows it to be malleable (for stainless steel the forging temperature is 2003ºF if magnetic and 2102 ºF if nonmagnetic) and then molded or shaped by applying force in the form of hammer blows or a press. Stainless steels work well in terms of forgeability, but because they remain strong at forging temperatures, they often require more hammer force and/or hammer blows than other alloys. The forging of stainless steels is used to make a number of manufactured parts for a variety of industries because of its exceptional resistance to corrosion. Due to its wide availability in most markets as well as its high level of strength and ductility, stainless steel is considered a great option for cost effective metal fabrication.
Titanium Forgings — Titanium forgings are the product of a metallurgical process in which titanium is given a particular shape by the application of a strong compressive force. The pressure applied during the metal forging process shapes the titanium and also causes plastic deformation in the grain structure of the metal, so that the grain flow follows the shape of the piece. Thus, forging is both an efficient way of forming titanium as well as a way to improve its directional strength.